MASTECS Technology use for the analysis of a Vehicle Domain Control Module (VDCM)
Marelli Europe s.p.a. – Powertrain division is in charge of the product area dealing with the whole vehicle’s propulsion system for ICE (Internal Combustion Engines) systems, inside Marelli group, one of the world’s leading global independent suppliers to the automotive sector, born from the fusion of Calsonic Kansei and Magneti Marelli
Marelli will deploy MASTECS technologies and tools for the analysis of a Vehicle Domain Control Module (VDCM). The VCDM is an integrated platform for Powertrain and Vehicle dynamic control. A high-level view of the diverse set of functionalities that can be managed by the VDCM is provided in the figure below. The VDCM system is compliant with the ISO26262 standard for Road Vehicle Functional Safety requirements, with the highest Automotive Safety Integrity Level (ASIL D).
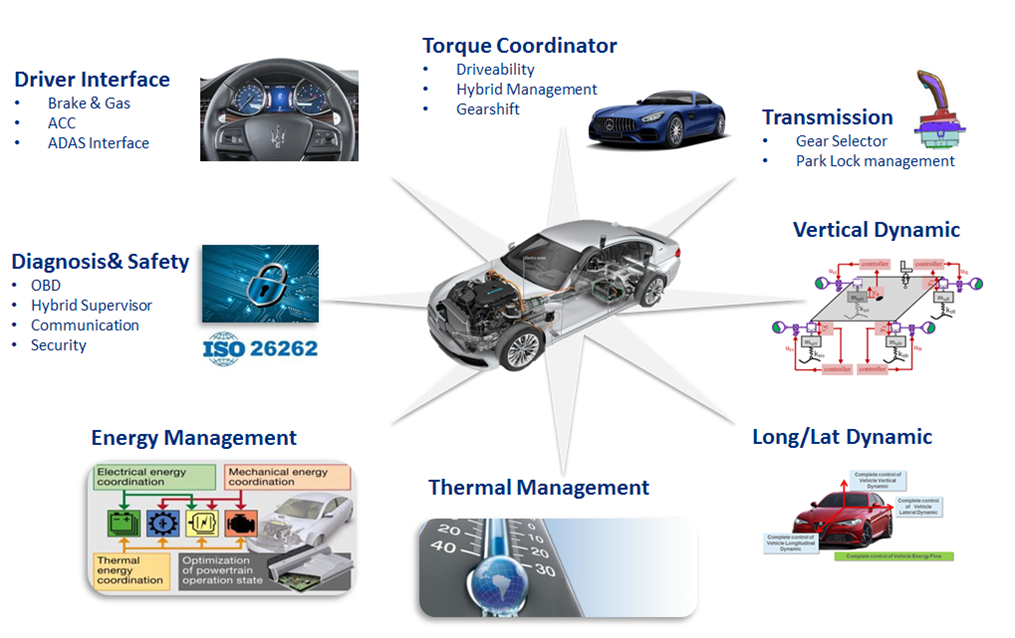
The system is configures by "Functions," where each function manages diverse aspects of the vehicle, ranging from canonical traction control functions to more cuttings ADAS Adaptive cruise control. The table below provides a hierarchical breakdown of main VDCM supported functions.
A schematic view of the system is depicted in the figure below, it shows how the VDCM ECU is connected to other vehicle's components as sensors, actuators, smart actuators, or other ECU.
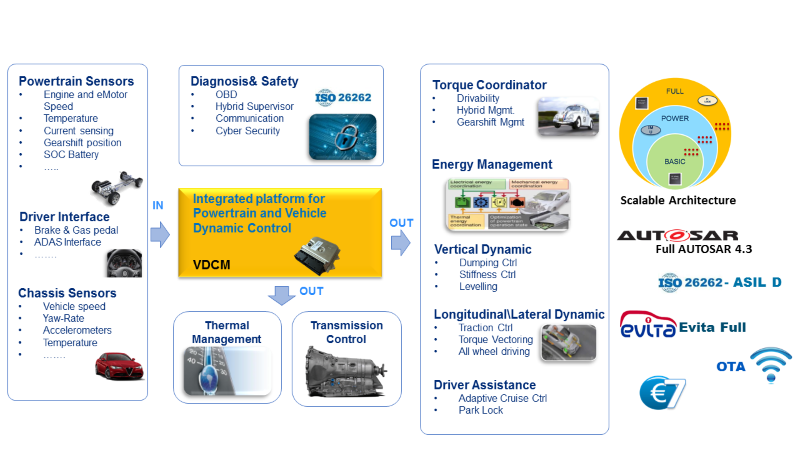
Overview of system connection
On the hardware side, the VDCM platform is based on 32-bit TriCore™ AURIX™– TC397 Microcontroller by Infineon with the following characteristics:
- 6 TriCore™ running at 300 MHz (with 4 additional checker cores delivering 4000 DMIPS).
- Supporting floating point and fix point with all cores.
- 16 MB flash/ ECC protection.
- Up to 6.9 MB SRAM/ ECC protection.
- 1 Gbit Ethernet.
- 12x CAN FD, 2x FlexRay, 12x ASCLIN, 6x QSPI, 2x I²C, 25x SENT, 4x PSI5, 1x PSI5S, 2x HSSL, 4x MSC, 1x eMMC/SDIOT, 1x I²S emulation.
- Redundant and diverse timer modules (GTM, CCU6, GPT12).
- EVITA Full HSM (ECC256 and SHA2).
- LFBGA-292 package.
- LFBGA-516 package.
- Developed and documented following ISO 26262/IEC61508 to support safety requirements up to ASIL-D/SIL3.
- AUTOSAR 4.2 support.
- Single voltage supply 5 V or 3.3 V.
- 165°C junction temperature.
From the software perspective, the VDCM architecture is based on Autosar 4.3 Conformance Class ICC3. VDCM is implemented as an Embedded Real Time Multitasking full preemptive Software, the management of scheduling and context is done by an OSEK Autosar compliant Operating System.
In the scope of MASTECS the VCDM will be initially release as a Single Core Application and developed into a multicore application. MASTECS technology will help Marelli in finding an efficient way to partition the Software on the different cores, as well as in supporting a multicore timing analysis framework addressing the verification and certification requirements of the VDCM, once deployed as a Multicore Application. Deploying VDCM as multicore application will also require the adaptation of the implemented Autosar Basic Software Architecture, as depicted in the figure below.
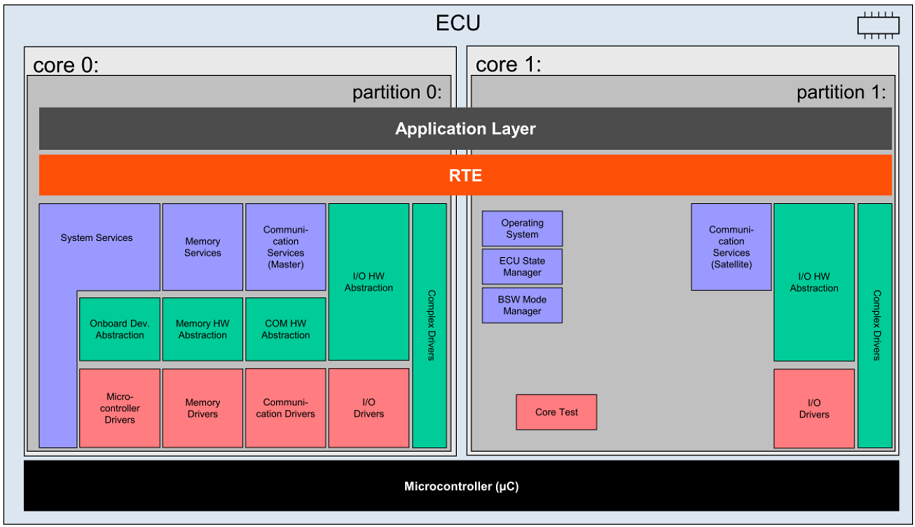
This document belongs to Marelli Europe SpA - Powertrain.
It may not be transmitted or communicated to any third party without prior authorization.